Filling Lines from Bottle Unscramblers to case Packers with Central Control Systems
Filling Lines from Bottle Unscramblers to case Packers with Central Control Systems
Filling lines from bottle unscramblers to case packers with central control systems involves a sophisticated process that ensures efficiency and accuracy in the packaging of products. Here's an overview of the key components and steps involved in this automated packaging system:
Bottle Unscrambler:
Purpose: Bottle unscramblers are machines designed to organize and orient bottles before they enter the filling line.
Operation: Bottles are fed into the unscrambler in a disorganized manner and are then sorted and positioned correctly for the filling process.
Filling Machine:
Purpose: Filling machines are responsible for accurately dispensing the product into individual bottles.
Operation: Bottles move along a conveyor system to the filling station, where a precise amount of product is dispensed into each bottle. This process can be achieved through various methods, such as gravity filling, volumetric filling, or piston filling.
Capping Machine:
Purpose: After filling, bottles may need to be sealed with caps or lids.
Operation: Bottles move to the capping machine, where caps are securely placed and tightened onto the bottles.
Labeling and Coding:
Purpose: Labels and codes are applied to the bottles for product identification and traceability.
Operation: Automated labeling machines affix labels to the bottles, and coding systems print batch numbers, expiration dates, or other relevant information.
Checkweigher:
Purpose: To ensure that each filled bottle has the correct amount of product.
Operation: Bottles pass through a checkweigher that measures their weight. Any bottles deviating from the specified weight range are rejected from the line.
Case Packer:
Purpose: Case packers are machines that pack filled bottles into cases for shipping and distribution.
Operation: Filled and capped bottles move to the case packing station, where they are arranged in the correct configuration and loaded into cases.
Central Control System:
Purpose: To manage and synchronize the entire packaging line.
Operation: A central control system oversees and coordinates the operation of each machine in the packaging line. It monitors and adjusts parameters, controls conveyor speeds, and ensures the seamless transfer of bottles from one station to another.
Quality Control Systems:
Purpose: To identify and reject defective products.
Operation: Integrated cameras or sensors can be employed for quality control. Bottles that do not meet specified criteria (e.g., incorrect fill level, missing cap) are automatically rejected from the line.
The integration of a central control system enables real-time monitoring, data collection, and adjustments to optimize the entire filling and packaging process. Additionally, it allows for quick identification and resolution of issues to minimize downtime and enhance overall efficiency.
Contact us for more information.
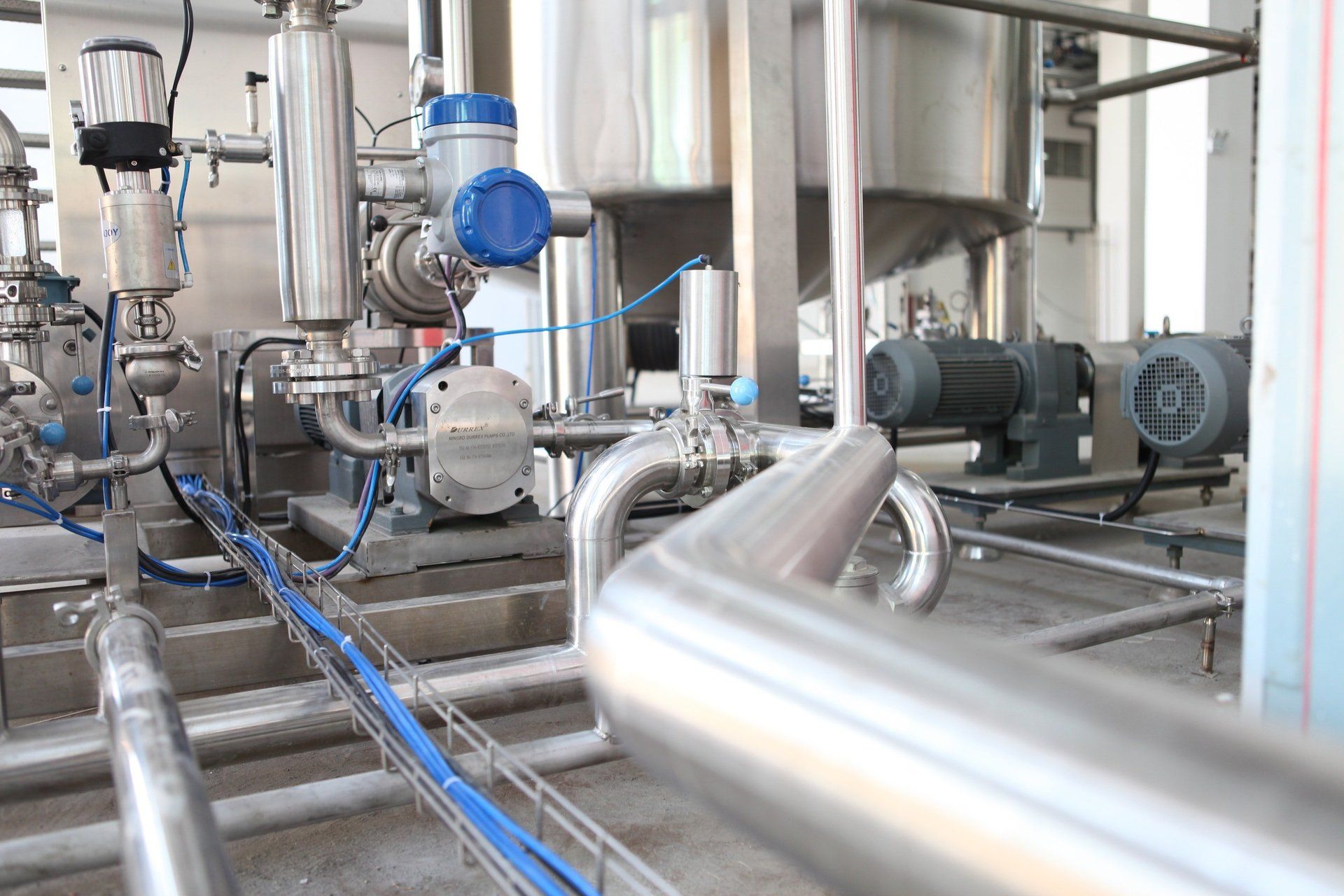
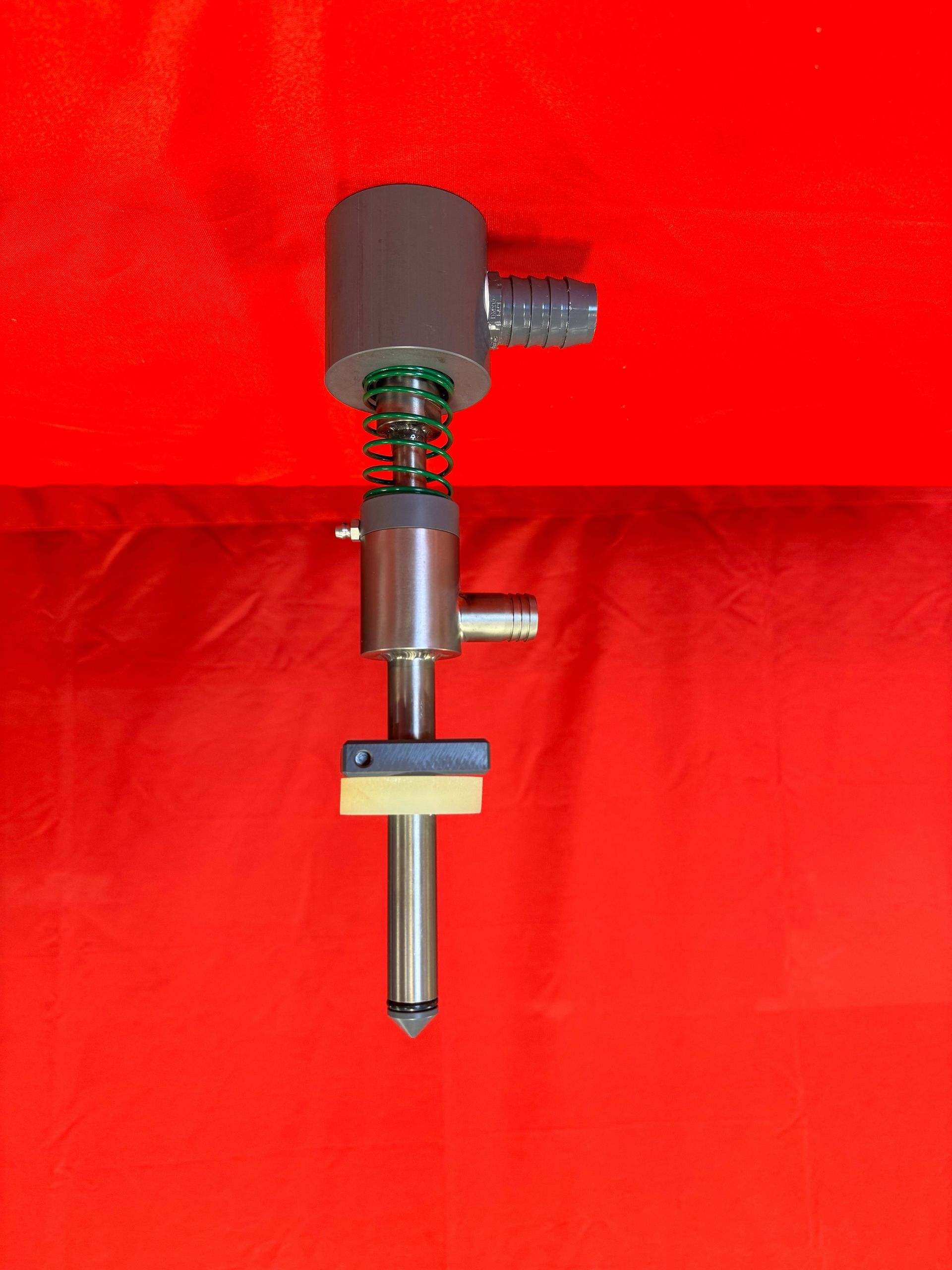